OVERVIEW
MMI’s design-centric mindset does not just encompass our manufacturing competencies, we believe that an in-depth understanding of the component design and its function that we manufacture in the millions gave us the competitive edge over our competitors.
Our value to our customers goes beyond our manufacturing competencies to positioning ourselves as a dependable partner that offers innovation and value to our customers’ product and thereby giving them an additional competitive edge in their market or industry.
COMPONENT DESIGN
A multi-disciplinary approach to component design is fundamental to our value proposition to customers. Because of the experience in the design and manufacture of a wide range of precision components of different manufacturing technologies we are able to offer our customers a holistic design drawn from the synergy of different domain expertise. It is this holistic integration of the different elements of design that makes MMI stand out from our competition.
Electro-magnetic Engineering
The Voice Coil Motor Assembly (VCMA) is a critical sub assembly of the hard disk drive (HDD) that MMI is the leading manufacturer in the industry. The VCMA is the power that drives the actuator for it to function in the HDD. A VCMA employs the leading magnet technologies. Introducing high performance magnets in a HDD that uses magnetic recording technology requires the Best-In-Class cleanroom manufacturing and control systems. Adding to the challenge, the modern HDD integrates the mechanical latches and crash stops into the VCMA sub system. MMI is always relied upon to provide a one-stop solution for VCMA supply for our customers.
The Structural Foundation
The base is the mechanical structure where all the components of the hard disk drive (HDD) are mounted and assembled. MMI has competency to manufacture and deliver the base whether the base is to be manufactured with extrusion, high speed precision casting and machined. Secondary processes like Epoxy Coating or Electro-less Nickel Plating are also integrated within MMI. To produce the base in high volume and ensuring reliability and quality, MMI uses numerous proprietary tooling and processes to ensure that our finished goods work seamlessly with our customers’ downstream processes that exceeded their expectations.
The Enclosure
The Top Cover together with the Base form the enclosure system for the Hard Disk Drive. Its primary function is to provide sealing, protection and robustness to the Hard Disk Drive. Apart from the above primary function, in today’s Permanent Helium Filled Hard Disk Drive, the Top Cover’s function went beyond the need of an air tight seal to a full hermitic seal.
The Top Cover secondary function can include acoustic treatment in the form of pre-laminated materials and/or dampers which can be implemented with different materials and damping adhesives.
TOOLING DESIGN
Tooling design is the heart of our passion in MMI. Our collective knowledge of component design and manufacturing processes are encapsulated into our tooling design. We are vertically integrated: From tooling concept and design, its fabrication, assembly and testing. This also includes servicing and spare parts fabrication which are also done in-house.
Apart from our competency in manufacturing tooling design, we also supported our customers early in the design and development in rapid prototyping to speed up design decisions and influence product design to ease into the manufacturing tool design. This gives the added value of time to market as well as time to volume for our customers.
PROCESS DESIGN
MMI is a dominant player in our industry since its infancy, we are pioneers in developing unique and robust processes that catered to the exacting demands of high-volume manufacturing that our customers have come to expect from us.
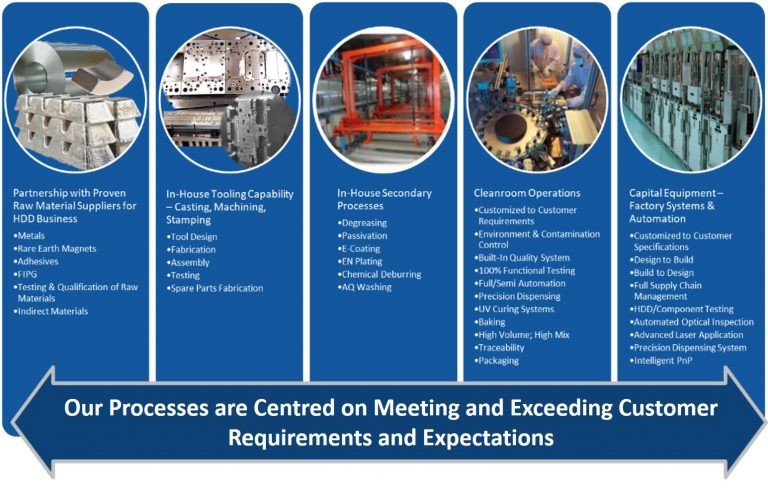
Our process design is centred around our customers’ requirements and needs. It starts upstream from how we process our raw materials right to the point our customers use our products.
Our customers will have access to a wide spectrum of manufacturing possibilities like, but not limited to, precision casting, stamping, forming and machining. Integrated with these manufacturing competencies are our range of secondary processes for surface treatment like aqueous cleaning, passivation, Electro-Depostion Coating, EN Plating, Chemical Deburring, and so on.
We also have Class 10,000; 1,000 and 100 cleanroom facilities to cater for specific customer requirements and needs for assembly operations. These facilities are highly automated and house advance processes like precision dispensing and curing systems, magnetization systems, baking and outgassing systems that meet or exceed hard disk drive (HDD) standards.
As an integrated multinational technologies company, we have the breadth and depth of manufacturing capabilities and proven process designs that deliver optimal value to our customers.
CAPITAL EQUIPMENT DESIGN
MMI offers a one-stop turnkey capital design for our customers. We appreciate that every customer has unique requirements in their capital equipment for manufacturing or testing. Requirements begin with the different standards, environment, how and where the equipment are to be deployed, how the equipment are to be evaluated. We do not stop here. Apart from successfully delivering and commissioning our customers’ capital equipment, equally important is the after-sales on-site service and support, spare parts availability and supply chain management which are all part of the total turnkey solution that MMI provides.
Automated Optical Inspection System
We employ the best-in-class vision systems and with our proprietary vision software, enabling customized solutions to our customers with a wide range of applications. Applications can include on or offline inspection, parametric measurement or visual inspection of parts to meet customers’ specifications.
Laser Application System
When optical inspection system are not applicable or suitable, MMI have strategic partners that we work with to co-develop advanced customized laser solutions to replace or complement optical inspection systems.
Intelligent Pick And Place
Our expertise in optical and laser application with state-of-the-art high speed process automation solutions and precision pick and place applications can be combined to handle a wide variety of different components assembly with in-line real time testing to match our customers’ manufacturing and safety requirements in different industries.
Dispensing Systems
MMI System Integration team has a track record of providing advanced dispensing and curing systems to different industries. Our fully automated systems are able to handle materials of various viscosities and flow rates or volumetric drop size requirements to deliver effective solutions for customers’ precision dispensing needs.
Industry 4.0
Smart factory deployment and integration is not new to the MMI System Integration team. Smart or intelligent manufacturing solutions can be built into our systems designs. With increased prevalence and affordability in sensing and IoT solutions, we are well positioned with our customers for Industry 4.0.